Katherine Wroth
Marketing Manager
Katherine Wroth is the Marketing Manager at Barrett Distribution Centers, where she is focused on amplifying the Barrett brand: our cutting-edge supply chain solutions, discussing the latest in tech logistics, and, of course, our most important asset, our people.
Katherine earned her Bachelor of Arts Degree in Public Relations & Advertising
More Content From Katherine Wroth
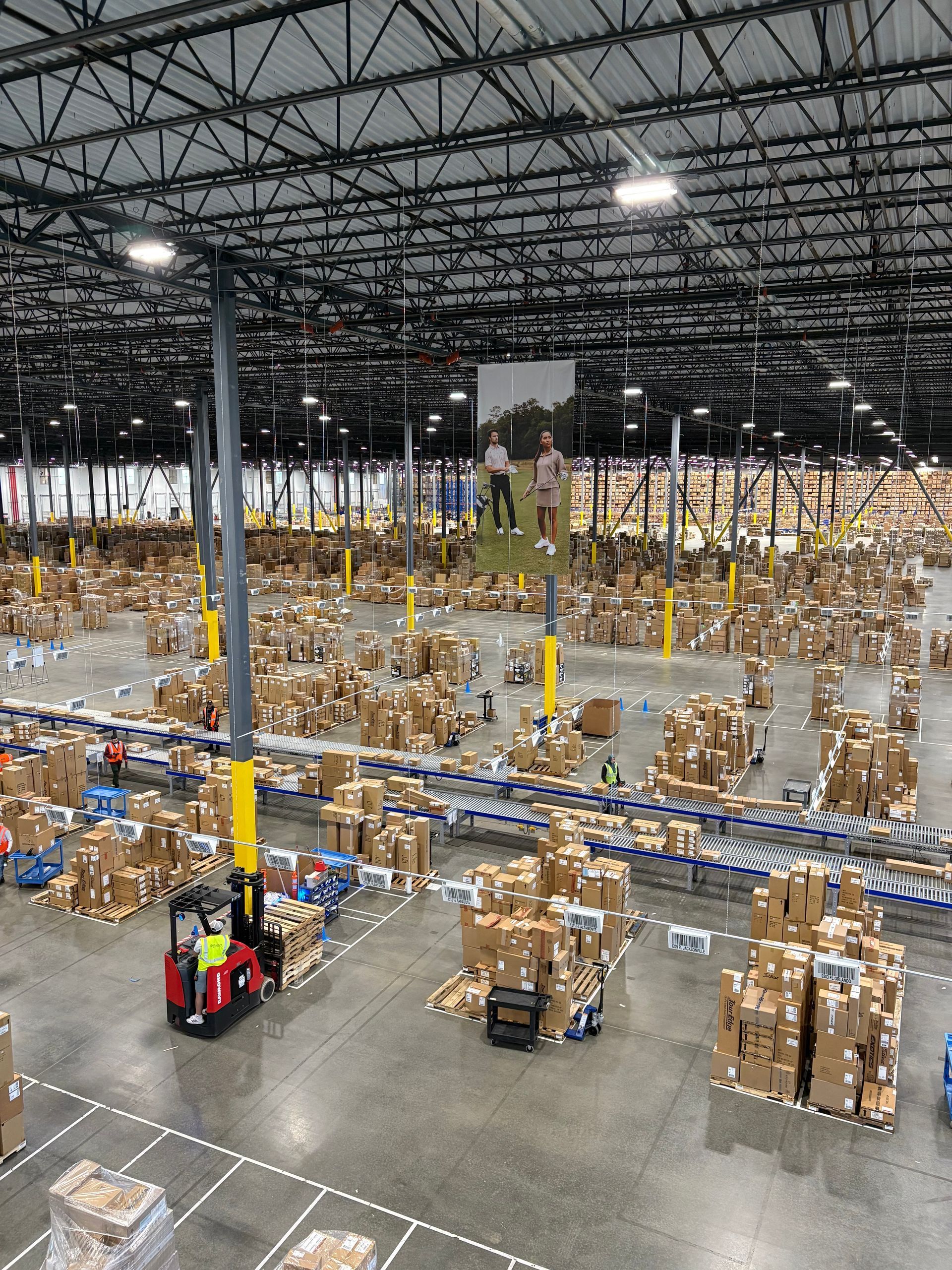
We’re nearly halfway through 2025, and eCommerce brands already feel the impact of major shifts in fulfillment, automation and consumer expectations. At Barrett Distribution Centers , we’re helping our partners stay agile and ahead of the curve. Here are four key trends and how Barrett delivers solutions that make a difference. 1. Brands Are Prioritizing U.S.-Based Fulfillment More Than Ever With global shipping delays, rising tariffs and increased regulatory complexity, the need for a dependable U.S. 3PL partner has become a top priority for growing brands. Many are rethinking their footprint and shifting volume back onshore to reduce risk and increase speed to the customer. How Barrett supports this: We operate over 25 strategically located fulfillment centers across the U.S., offering scalable support from coast to coast. Whether brands need to supplement an international setup or build a full domestic distribution strategy, we’re creating flexible models to meet their needs. What we’re hearing: More brands are asking for dual-node fulfillment strategies to shorten delivery windows and improve regional responsiveness, especially heading into peak season. 2. Smart Bundling is Beating the Shipping Rate Surge Shipping rates—especially for lightweight packages under one pound—continue to rise, with increases of 18–25% hitting hard in Q1 and Q2. Brands that haven’t yet adapted are seeing margin pressure grow. What Barrett is doing: We’ve helped several partners redesign their packaging, consolidate SKUs into bundles and reconfigure order logic to optimize shipping brackets. Our fulfillment and support teams work with brands to test and implement smart bundling strategies that lower costs while driving customer value. Quick win: Bundling offsets shipping costs, boosts average order value and makes promotions more profitable. 3. Automation Is No Longer Optional Warehouse automation isn’t just for enterprise brands anymore. With labor challenges and service-level expectations higher than ever, automation has become a necessity, especially for brands navigating rapid growth. Barrett’s approach: We use automation in facilities where it makes the most significant operational impact. These aren’t million-dollar systems; they’re right-sized tools that improve accuracy, reduce cycle time and speed up fulfillment. What’s changed in 2025: Automation has become more plug-and-play and faster to implement, meaning brands can see ROI within months, not years. 4. Personalization Is Driving Loyalty (and Repeat Orders) In 2025, personalization has shifted from “nice to have” to a competitive necessity. Customers expect a tailored experience, from the products to the packaging they arrive in. What Barrett delivers: We offer a full suite of value-added services, including embroidery, engraving, branded inserts, custom pack-outs and influencer kits. Whether you’re a luxury brand or a high-growth DTC company, we help create a fulfillment experience that feels on-brand and memorable. Why it matters now: As consumer spending tightens, brands that deliver on the details see higher customer lifetime value and stronger repeat purchase behavior. Looking for a True Partner—Not Just a Provider? The pace of 2025 isn’t slowing down. If your current 3PL isn’t keeping up, it may be time for a change. At Barrett, we combine hands-on operational excellence with strategic insight to help brands scale smarter. Let’s talk—schedule your complimentary supply chain consultation here.
For direct-to-consumer (DTC) brands, success begins in the warehouse. From the moment an order is placed, your fulfillment process shapes the brand experience. At Barrett Distribution Centers , logistics isn’t just backend support. Fulfillment is the heartbeat of a successful DTC brand. Here’s how your warehouse strategy directly influences brand loyalty, repeat purchases and those all-important unboxing moments. 1. Customer Expectations Have Changed — Fulfillment Has to Keep Up If a brand promises 2-day shipping, customers will instantly notice the moment it’s late. If they order a personalized item, they’ll remember if it arrives incorrectly. Your warehouse is responsible for: Speed to ship Order accuracy Inventory visibility Packaging quality These are no longer “nice to haves,” they’re part of your brand promise. 2. Repeat Purchases Are Won (or Lost) in Fulfillment Acquiring a new customer is expensive. Keeping them? That comes down to the post-purchase experience. When fulfillment runs smoothly, your customer gets: A fast delivery The right items A well-presented package Confidence in your brand And when it doesn’t? You risk returns, negative reviews and churn . Fulfillment is where trust is built (or broken.) 3. Unboxing Is a Brand Moment — Not Just a Shipping Step Think of unboxing as your final marketing impression. Are your products arriving in a beat-up box with packing tape and nothing else? Or are they arriving in a branded, curated, thoughtful way? DTC brands that go the extra mile with: Custom packaging Personal notes Kitting or gift sets Branded tissue or wraps ...are the ones customers share on social media and return to. Barrett’s value-added services make this scalable and seamless. 4. Scalability Matters More Than You Think A fulfillment strategy that worked when you were shipping 100 orders a month won’t work when you hit 5,000. The right 3PL helps you: Flex your labor during peak Open new nodes to reduce ship times Avoid stockouts and overstocks Plan for long-term growth Scaling without sacrificing service? That’s the difference between brands that burn out and break through. 5. The Right Fulfillment Partner Makes It All Happen At Barrett, we help high-growth DTC brands deliver on their promises. With 25+ facilities nationwide, personalized service, and a tech-forward approach, we offer the flexibility and support growing brands need. Whether you need: Custom packaging Subscription box fulfillment Multi-node distribution Seamless system integrations We build solutions that keep you agile, accurate and customer-obsessed. Ready to Scale the Right Way? Let’s discuss how Barrett can help your DTC brand grow smarter, ship faster, and stand out where it counts—from cart to customer. Contact us today for a complimentary supply chain consultation.